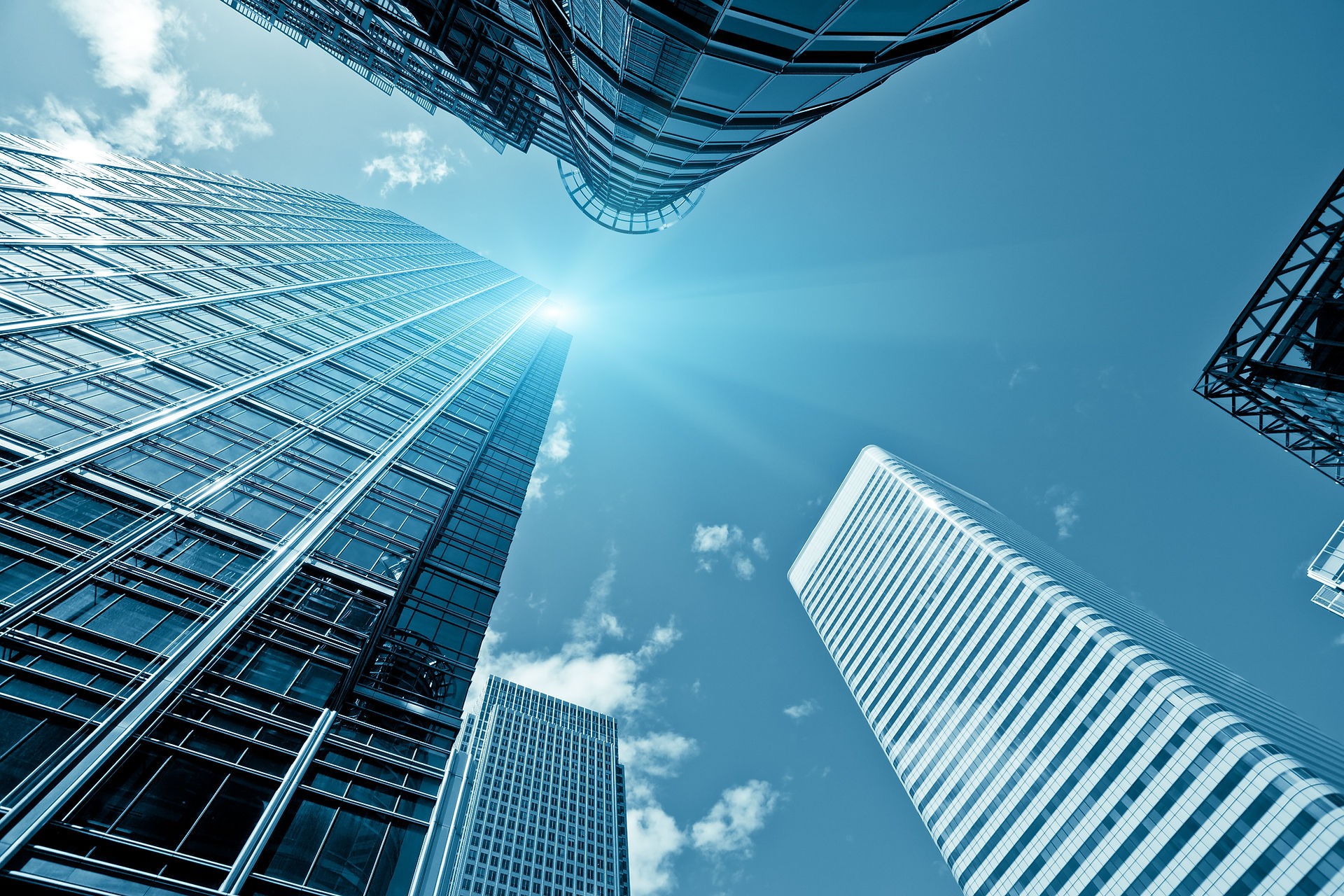
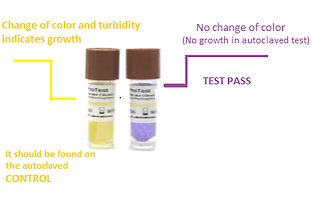
BIOLOGICAL TESTING
Prior to the 2003 edition of AS4815 The Centre for Disease, Control and Prevention (CDC) specified that:
Biological indicators (BIs) are the most accepted means of monitoring the sterilization process because they directly determine whether the most resistant microorganisms (e.g., Geobacillus or Bacillus species) are present rather than merely determine whether the physical and chemical conditions necessary for sterilization are met. Because spores used in BIs are more resistant and present in greater numbers than are the common microbial contaminants found on patient care equipment, an inactivated BI indicates that other potential pathogens in the load have also been killed.
Biological Indicators (BI's) are Class 5 indicators. They are simulating indicators which means their role is to replicate an environmental condition in a challenge process.
When AS4815 was released in 2003 there were many implications within this standard for sterilisation monitoring processes. One of the main amendments to Australian Standards Infection Control in both AS4815 and AS4187 was the removal of the mandatory use of Class 5 Biological Indicators. The reason for this was because international manufacturers now had the technology to be able to develop and manufacture intuitive sterilisers, particularly Class B or Class 2 type Bench Top sterilisers which could produce a chart printout of the necessary parameters required for sterility. Each day, prior to the batch run, the steriliser would perform a Daily Air Removal Test which is one of the four main parameters in sterilisation.
The chart printout would provide all of the necessary information required to prove that the steriliser met all four parameters prior to the batch run being loaded initially for the day, more information than a Biological Test would be able to provide, hence it became unnecessary to run Biologicals.
Today AS4815 and AS4187 require biologicals to be run for VALIDATION ONLY. Validation is required when a steriliser's mechanisms are altered in any way. This is usually done by the service technician on a 6-12 month bases. As part of annual Preventative Maintenance, technicians perform several checks on the sterilisers which usually include calibration of components inside the steriliser. This, in turn would then require checks to be done to ensure that the steriliser still functions correctly and responds correctly and accurately to actions initiated by the end user. To test the efficacy of the steriliser, the technician requires the checks made to be validated and to do this a spore population must be released into the chamber for testing and validation.
There is no mandatory requirement for an end user (non service technician) to perform biological class 5 tests. This is referenced in AS4815/4187 to ISO11138 as a normative reference.